Why Supply Chain Management is Important in an Organization
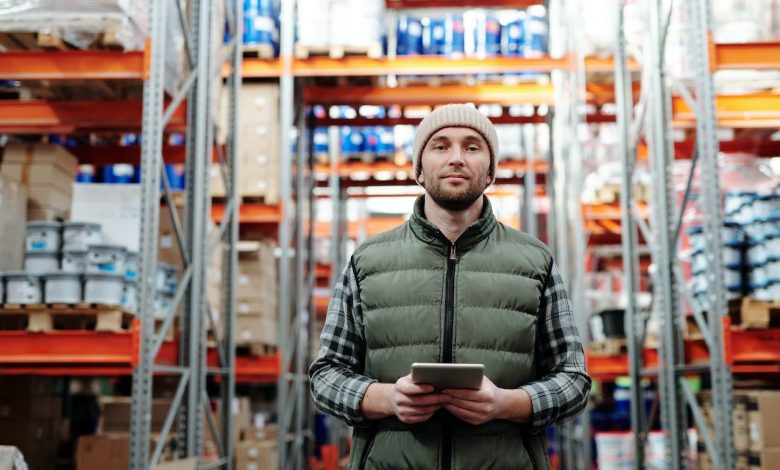
The modern market dictates its own rules. It is not enough to produce a quality product and provide it with marketing support to make a profit today. It is necessary to develop an effective scheme of product distribution. Thus, logistics plays the role of a strategic resource, and effective supply chain management, including supply chain automation, becomes a “magic wand”.
Why you need effective supply chain management?
The formation of global chains, the increase in competition serves as an impetus for the rapid development of integrated logistics. The inefficient organization of the commodity distribution chain often causes many problems, such as:
- losses in the assortment;
- lost profit from unsold goods;
- expenses for payment of fines;
- freezing of funds in the form of goods in long-term storage;
- loss of saleable condition for some goods and sale of goods at discounted prices.
Organizations gain a strong competitive advantage by improving strategic supply chain management processes and turning them into powerful assets.
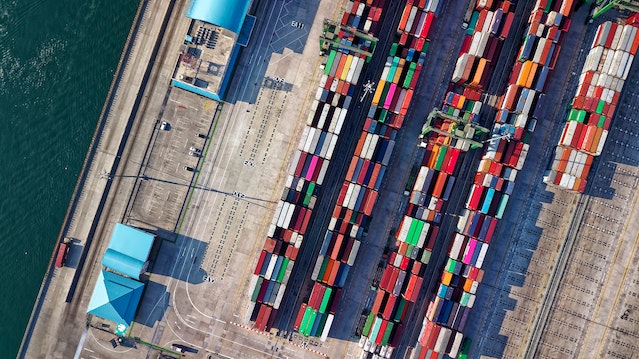
Important supply chain parameters
Effective supply chain management presupposes the presence of performance indicators common to all participants in the chain, which allow tracking the development of the chain in the right direction. The performance indicators should take into account both the specifics of the product and the stages of its life cycle. For example, the need of pallets for automated warehouses.
The following supply chain parameters are distinguished:
- The speed of the chain is the length of the cycle from the purchase of raw materials by the supplier of the goods to the receipt of the finished goods by the consumer. It is measured in days.
- Chain reliability: it is the degree of compliance with the established delivery dates.
- Chain flexibility is the ability to adapt the supply chain in a timely manner in accordance with the changing demands of the consumer.
- Chain costs are the total cost of the supply chain functioning, which consists of the costs of production, procurement, transportation, warehousing, insurance, write–off of obsolete and spoiled stocks, chain financing and many others.
The ideal supply chain should strive to achieve perfection in all these parameters. Unfortunately, this scenario is somewhat utopian.
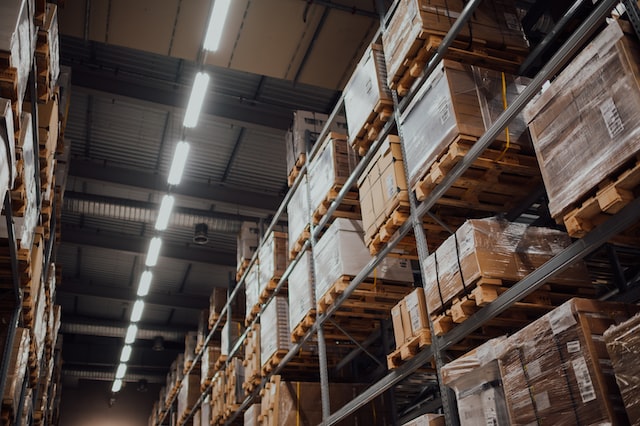
Increasing the reliability of the chain requires more careful planning and control, which automatically increases the corresponding investment in technology, training and coordination. Ensuring the speed of reaction forces companies to maintain stocks, which increases the cost of warehousing and increases the risk of writing off obsolete stocks. Increasing flexibility requires the introduction of flexible manufacturing technologies, which causes an increase in the cost of reconfiguring production lines and increases the percentage of production losses.
Improvement of one of these parameters, as a rule, leads to deterioration of the other. Meanwhile, the parameters of the supply chain change in a certain way throughout the product life cycle. Taking into account these patterns allows the product manager to identify the critical characteristics of the chain at a particular stage of the product life cycle. If it is impossible to achieve perfection in all parameters, the success of the supply chain is determined by the focus on the right parameters.